Monitoring liquid levels in industrial and environmental systems is critical for maintaining operational efficiency and safety. Whether you’re managing a water treatment facility, a chemical plant, or any operation involving liquids, having accurate and reliable tools for liquid level monitoring is key. These tools help prevent overflows, leaks, and operational disruptions. This guide explores the essential features of liquid-level monitoring tools, offering insights into their functionality and benefits.
Pipeline Support
One of the most crucial features of liquid-level monitoring tools is their ability to integrate seamlessly with existing infrastructure. The tools should offer robust pipeline support in wastewater when monitoring wastewater systems. This allows for efficient detection of blockages, leaks, or system failures in pipelines, which is essential for timely maintenance and risk mitigation. Proper support for pipelines enhances the monitoring system’s accuracy and ensures that operators can respond quickly to any irregularities that may arise in the flow of wastewater.
Accuracy and Precision in Measurement
For liquid-level monitoring systems to be effective, accuracy and precision are non-negotiable. These systems should provide real-time, accurate measurements to prevent any potential hazards. Whether you’re monitoring a tank, reservoir, or industrial container, the precision of these measurements ensures that the right actions are taken before any issues escalate. The technology behind these systems should be capable of detecting even the smallest fluctuations in liquid levels to maintain a stable environment.
Adaptability to Various Liquids
Another key feature to look for is the adaptability of the liquid level monitoring system to different types of liquids. Liquids vary greatly in their composition, density, and chemical properties, which can impact how the monitoring tools interact with them.
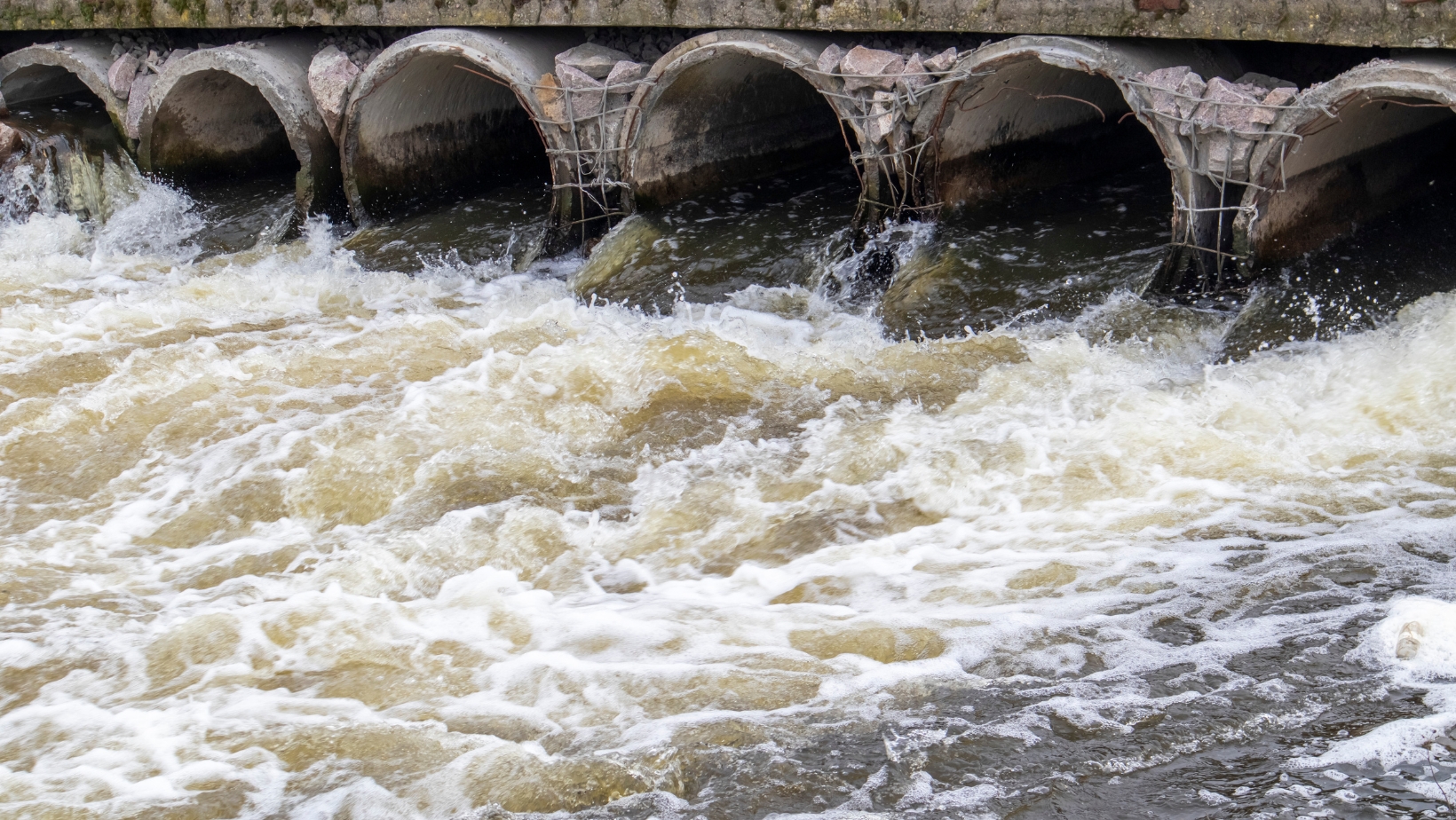
A good monitoring system should be designed to handle both hazardous and non-hazardous liquids, including oils, chemicals, and water. This adaptability ensures that the tool remains useful across a wide range of industries and applications, giving operators the flexibility to monitor various liquids without worrying about compatibility issues.
Remote Monitoring Capabilities
In an increasingly digital world, remote monitoring capabilities are becoming a necessity. These systems should allow for constant observation of liquid levels from a central control room or via a mobile device. Remote monitoring allows operators to monitor several sites simultaneously, increasing efficiency and reducing the need for frequent on-site inspections. This functionality is particularly valuable in critical industries where immediate response times are crucial for safety and regulatory compliance.
Integration with Alarm Systems
Liquid-level monitoring systems should be equipped with alarm functions to alert operators to any irregularities. These alarms can be configured to notify personnel when a tank or reservoir reaches a certain level, signaling a potential overflow or need for maintenance. These alarms can be visual, auditory, or sent directly to mobile devices, ensuring that operators are aware of any potential risks as soon as they arise. The ability to integrate with existing alarm systems, including automated responses to prevent overflow or spillage, increases safety and operational efficiency.
Long-Term Durability and Maintenance
The long-term durability and ease of maintenance of liquid-level monitoring systems are crucial considerations for industries that rely on these tools for consistent, uninterrupted operation. In many industrial environments, the conditions can be harsh, with extreme temperatures, exposure to corrosive chemicals, and mechanical stresses that could potentially affect the functionality of the monitoring system. A durable liquid-level monitoring tool should be constructed from materials that can withstand these harsh conditions, whether it’s high temperatures, corrosive liquids, or physical impacts. Corrosion-resistant metals and durable plastic components are often used to ensure longevity. These systems should be designed for minimal maintenance to reduce downtime and the need for frequent repairs.
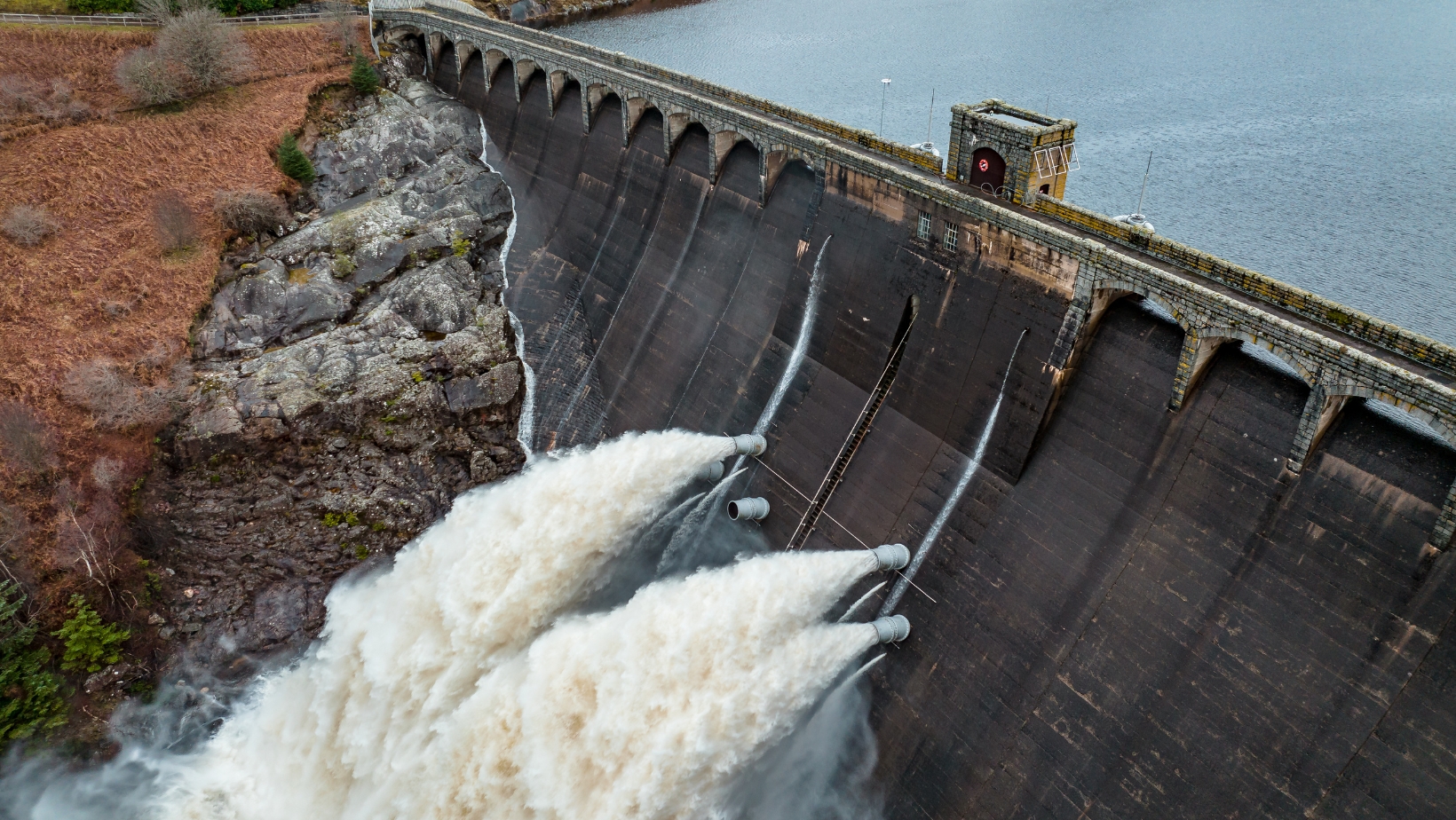
Regular maintenance can be costly and disruptive, so systems that require fewer interventions not only lower operational costs but also ensure that liquid-level monitoring remains reliable over time. One important factor is the ease of access for cleaning, inspection, and part replacement; systems designed with user-friendly maintenance in mind can make upkeep simpler and less time-consuming.
Cost-Effectiveness and Return on Investment
Finally, cost-effectiveness is an important consideration when selecting liquid-level monitoring tools. While it’s tempting to opt for the cheapest option, the overall value of the system should be assessed. A higher initial investment in a more reliable and durable system can result in long-term savings by preventing costly spills, system failures, or downtime. Additionally, systems that offer lower maintenance costs and longer lifespans are more cost-effective in the long run. The true return on investment comes not just from the purchase price but from the potential to avoid risks and optimize operations.
When choosing liquid-level monitoring tools, it’s essential to look for features that ensure accuracy, adaptability, and durability. From pipeline support to remote monitoring capabilities and system integration, these tools play a pivotal role in maintaining operational safety and efficiency. By considering these key features, industries can make informed decisions that not only prevent costly disruptions but also enhance the overall functionality of their systems.